Anbody attempt this? I built lh wing in sequential order. The right hand has the autopilot servo, so I temporary installed and rigged the aileron/flap prior to installing the two bottom skins.
I could simply remove the rods and reinstall after "skinning " the bottom of the rh wing....or it doesnt look like access is more restricted with those items left installed
(wiring not secured yet)
Advice?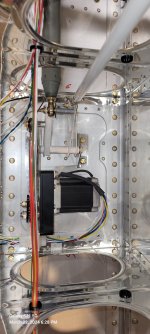
I could simply remove the rods and reinstall after "skinning " the bottom of the rh wing....or it doesnt look like access is more restricted with those items left installed
(wiring not secured yet)
Advice?
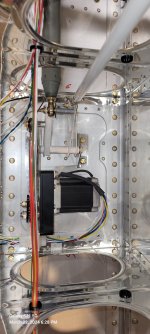