charlesmc
Member
Hi - Looking for critiques of our RV-10 power wiring diagram. I've put together multiple block diagrams including ones based on Z-13, Z-14, and Z-101. However, Bill Judge forwarded me a presentation that he gave that included a "get home" configuration that seemed really interesting. We're keeping it at a block diagram level now and will go into further detail once we get general consensus on the block diagram. We've also been debating a Z-14 approach.
As background, my partner and I are coming from a C-182 club where we lost an alternator approximately every six months. We had alternator failures at night, in IMC (2X), first thing on an engine break-in flight, on a commercial check ride, and my partner was stranded on a long cross-country. So, we are looking to create a very robust system as we fly a fair amount of IFR and we are very sensitive to alternator failures based on prior experience.
Things we have decided on already (we have done our research on these items) - dual ETX batteries, VPX, 60A primary alternator, 30A Monkworkz backup generator, P-MAGs.
The top image is a slide from the Bill Judge presentation. The bottom is our block diagram that we are hoping to get feedback on. Any mistakes in implementing Bill's circuit are completely my own.
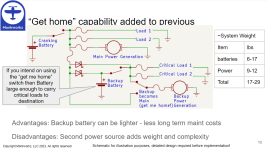
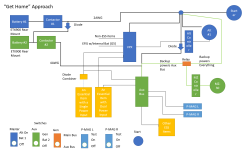
As background, my partner and I are coming from a C-182 club where we lost an alternator approximately every six months. We had alternator failures at night, in IMC (2X), first thing on an engine break-in flight, on a commercial check ride, and my partner was stranded on a long cross-country. So, we are looking to create a very robust system as we fly a fair amount of IFR and we are very sensitive to alternator failures based on prior experience.
Things we have decided on already (we have done our research on these items) - dual ETX batteries, VPX, 60A primary alternator, 30A Monkworkz backup generator, P-MAGs.
The top image is a slide from the Bill Judge presentation. The bottom is our block diagram that we are hoping to get feedback on. Any mistakes in implementing Bill's circuit are completely my own.
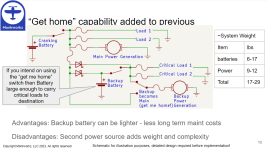
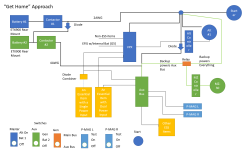