I'm working up to starting on my electrical design for my RV-10 build and I had a few basic preliminary questions. I have read the AeroElectric book and have a pretty strong electrical background.
1) It feels like there should be a clear answer on how to handle grounding in an aluminum aircraft, yet I can't find that clear answer. For example:
2) I thought about putting in an external/ground power connector to (1) jumpstart the plane if the battery is dead and (2) to provide power for setting up and configuring the avionics. I don't love the idea of adding a custom external connector, and I'm not clear on what plug standard I would use for this. So, alternatively, I'm thinking about putting external battery terminals in the cargo area with a cover, connected directly to the battery. I could connect any battery charger or jumper cables to these to accomplish the same thing.
Question: I have seen some electrical diagrams with a ground power port, and every one of them has a contactor for the ground power. Why is that? Is it just to prevent the terminals from being energized when not in use? Do I need a contactor if I do this? I'm thinking something like this in the cargo area:
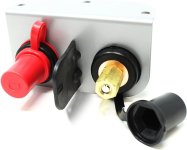
1) It feels like there should be a clear answer on how to handle grounding in an aluminum aircraft, yet I can't find that clear answer. For example:
- In the FlyEFII installation manual (something I'm considering), it definitively says that there should be a single ground bus hardwired to the battery
- But the RV-14 kit comes with wiring harnesses that utilize the chassis as the ground
2) I thought about putting in an external/ground power connector to (1) jumpstart the plane if the battery is dead and (2) to provide power for setting up and configuring the avionics. I don't love the idea of adding a custom external connector, and I'm not clear on what plug standard I would use for this. So, alternatively, I'm thinking about putting external battery terminals in the cargo area with a cover, connected directly to the battery. I could connect any battery charger or jumper cables to these to accomplish the same thing.
Question: I have seen some electrical diagrams with a ground power port, and every one of them has a contactor for the ground power. Why is that? Is it just to prevent the terminals from being energized when not in use? Do I need a contactor if I do this? I'm thinking something like this in the cargo area:
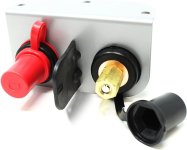